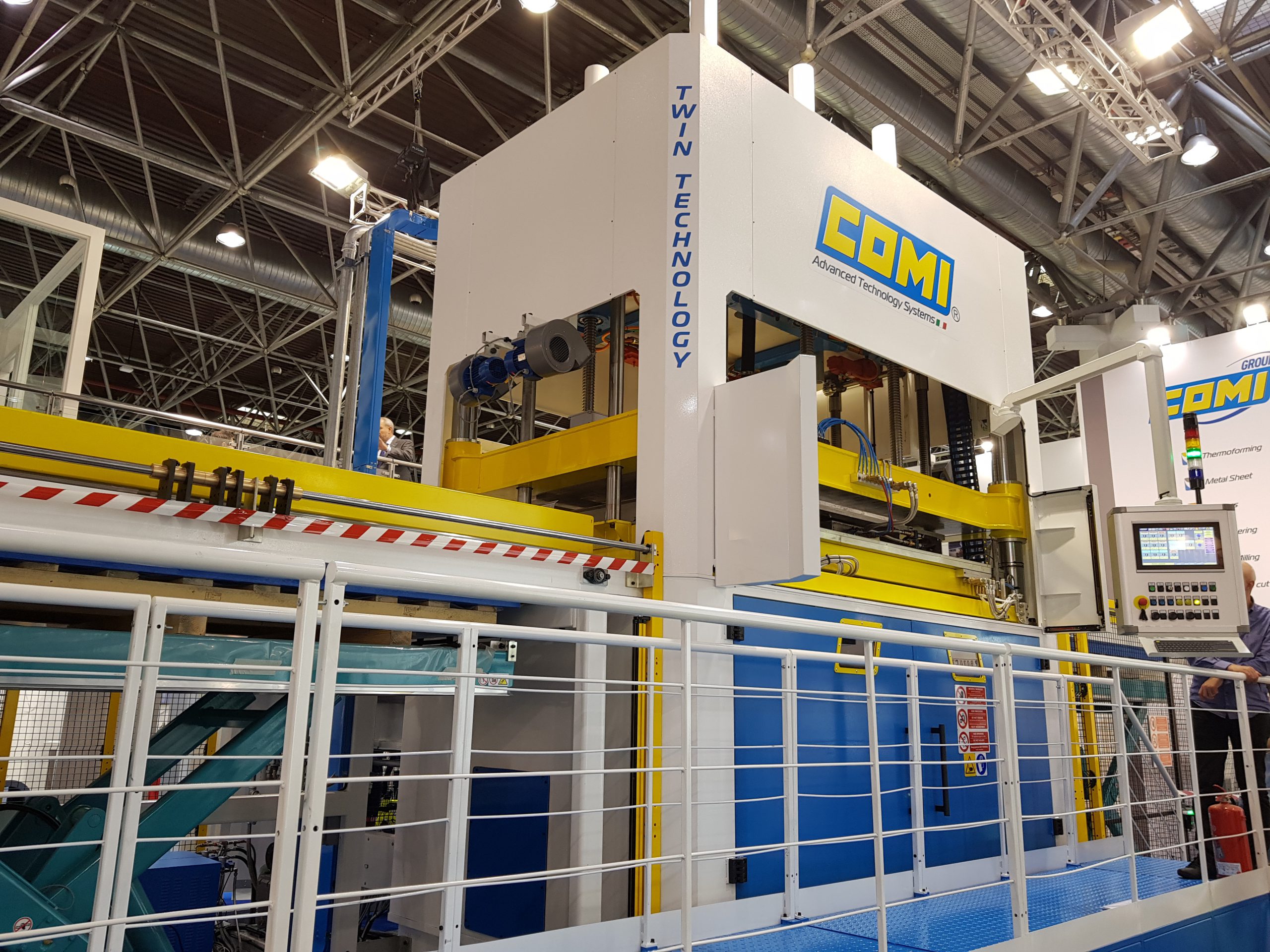
14 Jan Machine of the month: TWIN SHEET TECHNOLOGY
TWIN SHEET TECHNOLOGY: A SINGLE STATION THERMOFORMING MACHINE THAT ALLOWS TO CONSIDERABLY INCREASE PRODUCTIVITY AS WELL AS FLEXIBILITY.
Self Group Comi is an industrial machinery manufacturer and new technologies promoter, holding a global leadership position in thermoforming machines employed in the manufacturing of refrigerators inner liners and inner doors. More than 2000 units are installed all around the world.
Established in 1973, Self Group Comi is today a diversified group capable to design and manufacture Thermoforming machines & Molds, Presses, CNC Milling and WaterJet and Laser cutting machines, Metal Sheet working systems.
Its special and standard machineries are widely used in Household appliances, Automotive, Aerospace, Railway, Mold making, Marine sectors.
Thanks to its Engineering Department Self Group Comi also integrates robot, laser and other new technologies in highly customized and automated working units. Guarantee the manufacturing solution with the highest performance in every working condition has been the Self Group Comi driven since it was born.
Through the development of important projects with the range today available and the acquisition of complementary technologies/partnership, Self Group Comi will pursue its growth towards a 360° offer to its customers.
THE WORLD OF THERMOFORMING
Self Group Comi, with more than 47 years of experience in thermoforming, is one of the most prestigious and recognized brands in the refrigerators manufacturing, appliances, automotive, sanitary and industrial sectors. Self Group Comi thermoforming machines are unique products on the market as they are completely customizable on the basis of customer requests. They are not standard machines, but have unique features and advanced technologies that decrease cycle times and increase the performance and productivity of the machine.
Comi produces 3 lines of thermoforming machines: in-line, single station and for packaging. In-line thermoforming machines are the most advanced and highly productive machines, they reach up to 170 thermoformed pieces per hour and have four/five stations: the loading area for material in sheets or reels, the heating area with one or two stations, the forming area with vacuum inside the mold or with pressure system. Finally the unloading station. Additionally Self Group Comi machines can be enriched by the cutting area with guillotine or press to finish the thermoformed piece. Instead the single station thermoforming machines, named Laborforma, are not highly productive but they are very versatile. In this process, plastification and forming take place together. The material loading/unloading is manual, or automatic if equipped with a specific optional. Molds forms can be positive or negative, relating to the material sliding line which are used.
The LaborForma thermoforming machines are suitable for working plastic materials HIPS / ABS / PMMA / PP in cycle, with thickness up to 12 mm.
If equipped with dedicated accessories, they can also process materials reel-to-reel up to approx. 2,5 mm.
These machines are suitable for the production of thermoformed items: for the bathroom furniture (bathtubs, tubs, shower trays, shower walls), household appliances (refrigerators, containers, vacuum cleaners), automotive parts, aerospace components, illuminated signs, helmets, etc.
Last but not least Self Group Comi, after the partnership with Amut, gave rise to the Amut-Comi brand highly specialized in the thermoforming sector for packaging.
These machines are divided into four production lines based on certain requirements on the production cycle. They produce trays, plates, lids, containers and jars in thermoplastic material such as BOPS, PP, PLA, rPET, APET, CPET, HIPS, EPS, PVC and barrier materials, as well as containers, trays and cups that will be used in vending machines.
TWIN TECHNOLOGY
The twin sheet thermoforming machine was presented at K Düsseldorf fair one year ago, it’s a single station but with a peculiarity.
Its process heats, forms and welds 2 sheets simultaneously. The material reaches the plasticization temperature thanks to the two heating panels which have a sandwich like disposition.
This technology allows to considerably increase productivity as well as flexibility.
What are the benefits and its peculiarity?
A considerable advantage of the twin-sheet process is that subsequent joining by bonding or welding is dispensed with, as well as a significant shorter cycle times achieved in the thermoforming machines with two heating panels or optionally with two separate stations, in which one sheet each can be heated bilaterally in each one.
Furthermore the slab cut inside the machine during the process that improves performance by increasing productivity and the machine can manufacture either door and base in twin sheets and roof and side pannels in single sheets.
How does its forming process work?
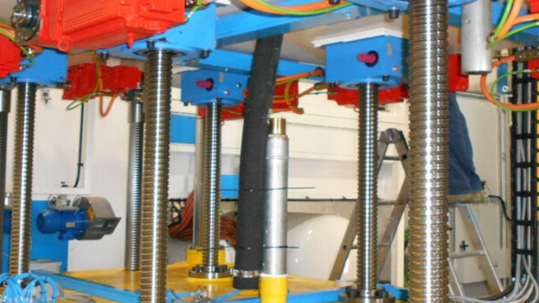
This process is used two sheets of material to create a cavity. It possible to insert between the two sheets pu foam or other component while the double-plate cools in the mold.
In forming a double sheet between two sheets of plastic are heated to processing temperature within frames, are mounted on two opposite mold plate with mobile devices for applying vacuum and pressure.
The two heated sheets are brought into the forming station between the two opposing dies. The mold plates are compressed on a processing temperature, with the edges matched claws held firm.
The pressure of the two dies that compress the plates at that point ties together perfectly, as they do in a heat-sealing pressure.
To complete the forming are the following groups: upper frame made of steel rods electrical movement with vertical opening; the upper frame will be equipped with mechanic blocks and six recirculation screws to weld and possibly cut; moulded piece cooling group through electric fans placed on the upper part of the machine structure (the number of the ventilators depends on the machine dimension); vacuum system equipped with tank and vane pump; proportional valves for bubble, vacuum and detachment phases with setting values which can be adjusted by PC and stored; photoelectric protection guards for the working area; safety panels and protections and back fan for the heating caisson cooling.
The machine control
The electrical board of the machine is equipped with one PLC Siemens S-1500, which regulates all the functions of the operating cycle (manual, automatic, safety, diagnostics) and which controls the heating through dedicated PLC HETRONIK, which is connected to it.
PLC Siemens is connected to one PC, placed at the front of the machine, to regulate all the functions of the operating cycle: manual functioning, automatic functioning and safety and diagnostic.
Doble automatic loader
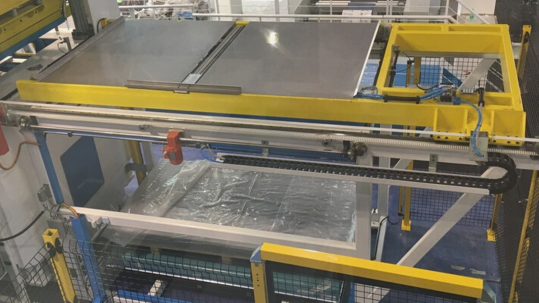
This group is laterally located to the thermoforming machine and is composed by two sheets loading areas placed one on the right and one on the left side.
Each loading area consists of : a sheet holder lower plan with vertical movement and a mobile plan composed by a suction cups holder motorized plan for the picking up of the sheet in the lower part and by a translation carriage to discharge the thermoformed pieces in the upper part.
During the automatic cycle, the moulded piece previously lifted is discharged on the top of the first carriage to be extracted from the forming station and moved to the unloading area.
Mould changeover
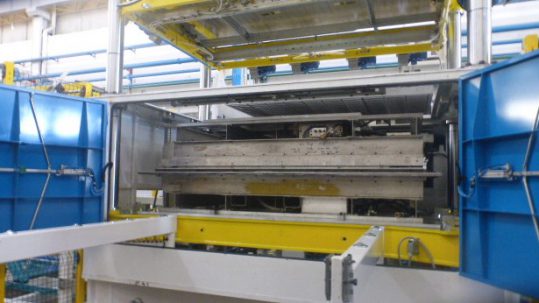
The mould changeover consists in: placing the mould, together with its lower reduction frame, on the moving table inside the caisson; and moving upward of the mould and automatic clamping of the lower reduction frame on the inner part of the caisson through two blades moved by pneumatic cylinders.
Remote assistance
It consists in allowing the total transfer of the machine PC control to the Self Group Comi assistance in real time. This gives the possibility to check all the machine functionalities: diagnostics, control and modifications on the system software, modification of parameters and calibration of the axes (drives), check of the general functioning data. The communication software with its proper licence is preinstalled and activated on the PC at the moment of running test. The only requirement that the customer must satisfy is the net connection (LAN or WiFi) to Internet.
Laborforma twin technology is suitable for those looking for high performance with greater production flexibility, a customized machine for every need.
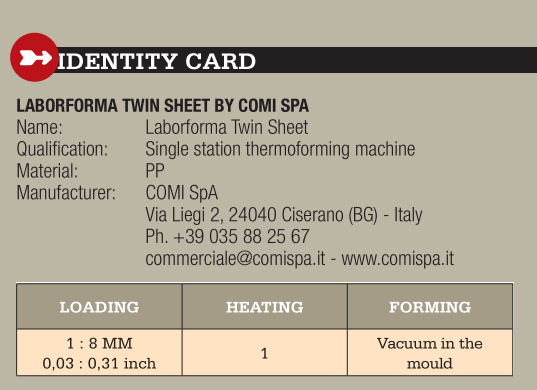